A Proud History Spanning Two Decades in the Rail Industry
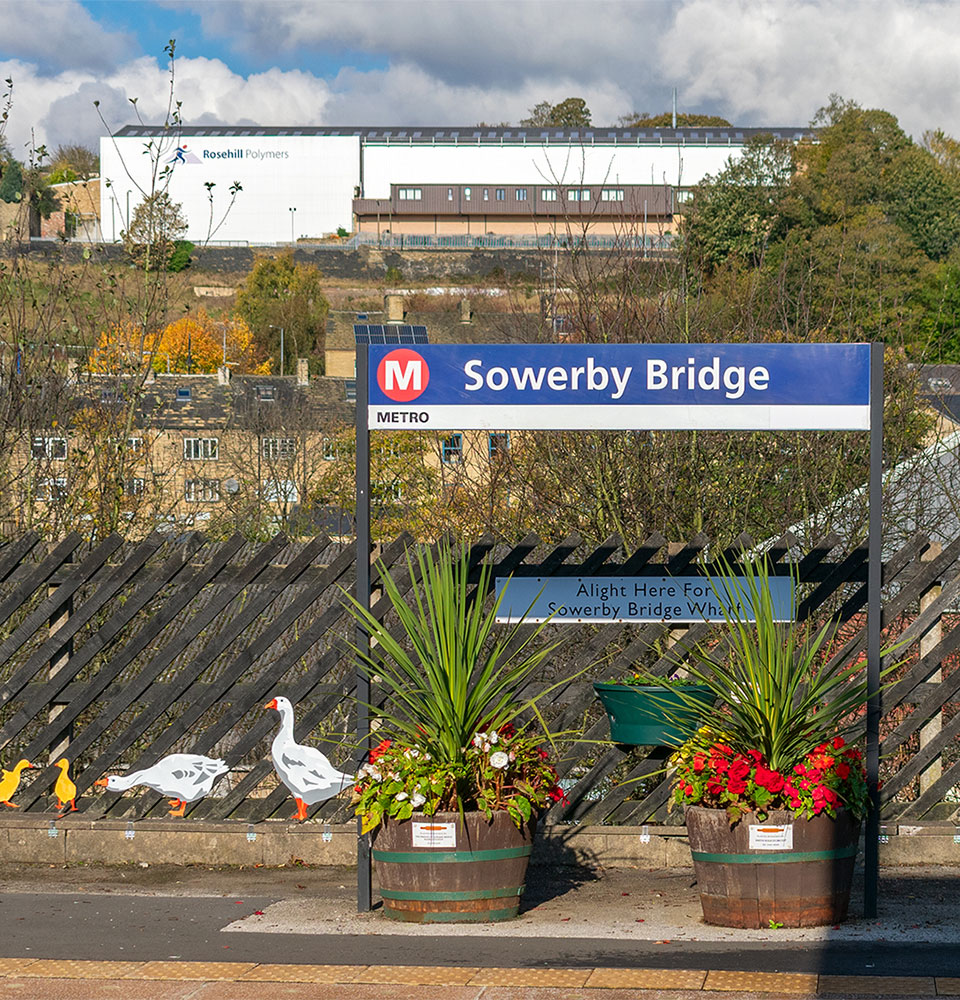
Discover Our Journey
The team at Rosehill embraced the challenge, conducting extensive testing and trials, which led to the successful development of a cold cure bonding process. This new method significantly reduced the curing time to just 1.5 hours, enhancing production efficiency and conserving energy. After Omni ceased production of their railway panels in 1999, Rosehill seized the opportunity to further their impact in the rail industry by purchasing Omni’s moulds and beginning their own production of railway crossing panels. This marked the start of Rosehill Rail, continuing the company’s dedication to innovation and sustainability in rail technology.
Bespoke Manufacturing Tailored to Your Needs
Quality
Our commitment to quality is underpinned by our adherence to the International Standard ISO9001:2008, with our quality assurance system rigorously audited annually by the National Quality Assurance (NQA). The manufacturing process benefits significantly from state-of-the-art computer control and is overseen by a team of highly trained, experienced professionals. Our plant and machinery, specifically designed and built for the production of railway crossing panels, are maintained under a dedicated contract by specialist engineers. This rigorous attention to detail and precision in every step of production ensures that we consistently deliver superior railway solutions tailored to the unique needs of our clients.
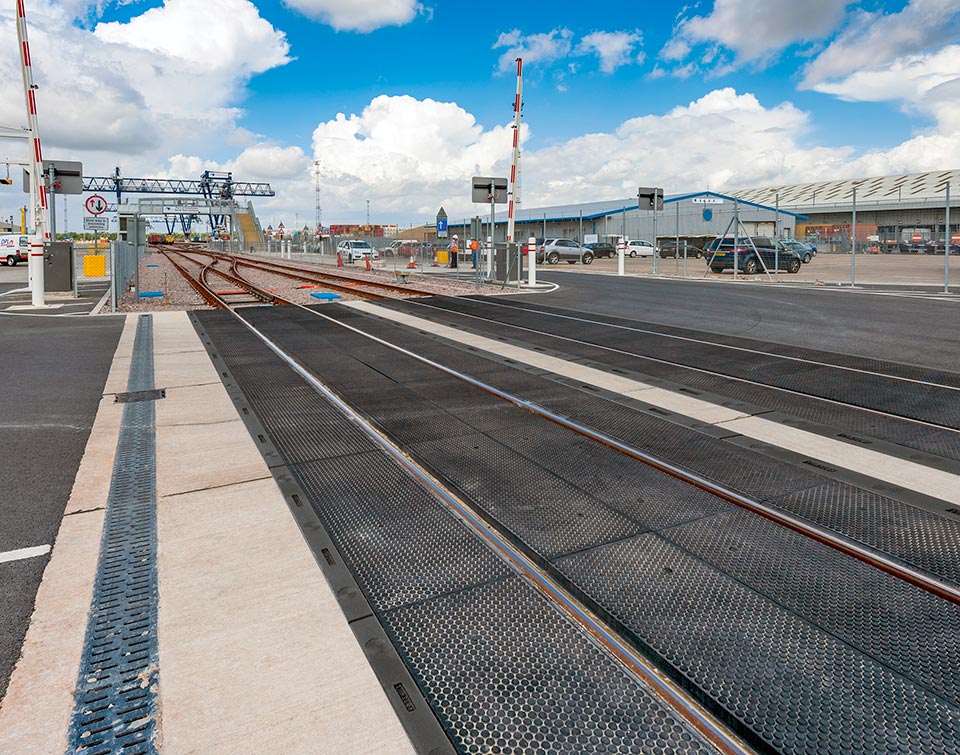
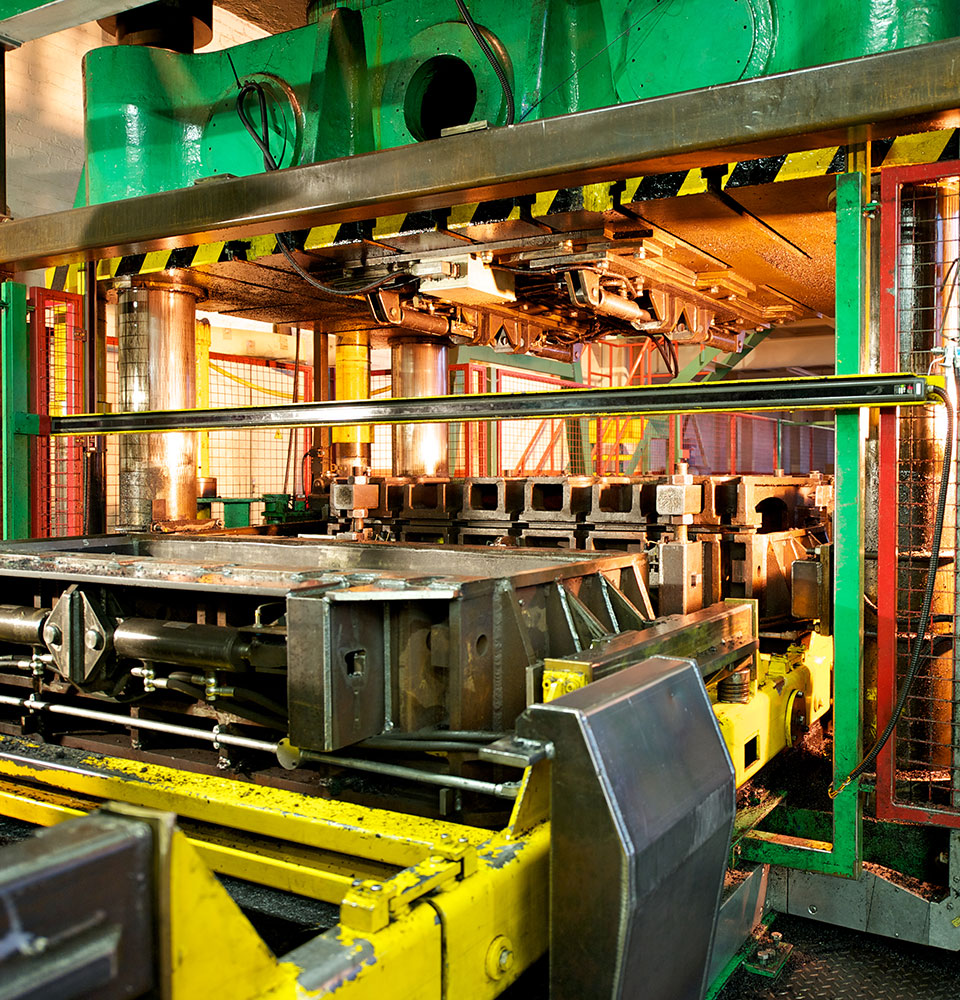
Reliable Traceability for Peace of Mind
Every panel is marked with essential information for quick identification:
Crossing grade | Rail type | Sleeper type | Fastener type | Year of manufacture
For example: ROAD UIC60 B70 SKL14 2011
This marking system enables engineers and site managers to swiftly verify that the panels meet the required specifications on-site.
Exclusive Design Rights
All components in our level crossing systems are designed by Rosehill Rail (a Division of Rosehill Polymers Limited), including those supplied under other names by our global distributors.
Environmentally Conscious
Rosehill Rail Crossing Panels pose no risk to the environment. They are manufactured using recycled rubber tyres, bonded together with an advanced polyurethane binder through a revolutionary, unique cold-cure manufacturing process.
Upon completion of the manufacturing process, the panels will not react with soil or water, nor will they leach chemicals into the environment or emit harmful vapours or odours into the atmosphere. Our commitment to sustainability ensures an eco-friendly solution for your rail needs.